Step-by-Step Guide to Understanding How a Paper Bag Making Machine Works
Release time:2025-05-05 Classification:Knowledge
A paper bag making machine is a specialized piece of equipment designed to automate the production of paper bags efficiently and sustainably. By converting raw paper rolls into finished bags, these machines streamline manufacturing processes while minimizing waste. Below, we break down the working mechanism of a paper bag making machine, detailing its key stages and operational principles.
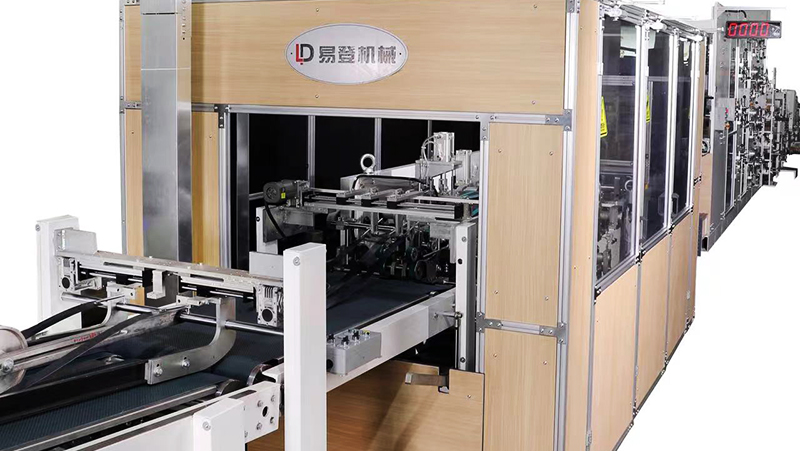
1. Unwinding the Paper Roll
The process begins with feeding a large roll of kraft paper or recycled paper into the machine. An unwinding unit carefully unwinds the paper, maintaining consistent tension to prevent tearing or misalignment. Sensors ensure smooth material flow, which is critical for maintaining production quality.
2. Printing (Optional)
If customized designs or branding are required, the paper passes through a printing unit. Flexographic or offset printing techniques apply logos, text, or patterns using eco-friendly inks. This step is fully adjustable to accommodate different colors and designs.
3. Die-Cutting and Creasing
Next, the paper moves to a die-cutting station, where sharp blades cut it into predefined shapes. Simultaneously, creasing wheels create fold lines to ensure precise folding later in the process. This stage determines the bag’s dimensions and handle cutouts (if applicable).
4. Forming the Tube Structure
The cut paper is folded vertically into a tubular shape. Adhesive is applied to one edge, and the overlapping sides are pressed together to form a seamless side seam. This step creates the bag’s basic structure.
5. Bottom Folding and Gluing
The machine folds the bottom of the tube inward, applying glue to secure the folds. Advanced machines use heat-activated adhesives for faster bonding. This step ensures the bag can hold weight without leakage.
6. Drying and Compression
The glued sections pass through a drying chamber, where hot air or UV curing solidifies the adhesive. Pneumatic presses then compress the bag to reinforce its shape and durability.
7. Handle Attachment (Optional)
For bags with handles, pre-cut paper handles or twisted cord handles are attached using adhesives or stitching. This step is automated for high-speed production.
8. Stacking and Packaging
Finished bags are counted and stacked automatically. They are then bundled into packs, ready for distribution.
Key Advantages of Modern Paper Bag Making Machines
- Speed and Efficiency: Automated systems produce thousands of bags per hour, reducing labor costs.
- Eco-Friendly: Optimized material usage minimizes waste, supporting sustainable manufacturing.
- Customization: Adjustable settings allow for variations in size, handle type, and print design.
- Durability: Precision engineering ensures consistent quality and load-bearing capacity.
A paper bag making machine integrates advanced mechanics, adhesives, and automation to transform flat paper into functional, eco-conscious bags. By understanding its step-by-step operation, manufacturers can optimize production lines to meet growing demand for sustainable packaging solutions. This technology plays a pivotal role in reducing plastic dependency while delivering high-quality, customizable paper bags.