Inline Printer
Inline Printer
Inline printing press for valve sacks and open-mouth paper bags
Inline printing combines the printing and bag-making processes in a single production line, reducing the time and labor costs between different steps. By completing both printing and bag forming on the same machine, it eliminates the time wasted on transportation, storage, and reprocessing, thus improving production efficiency.
The valve bag tuber machine connected with the inline printer is used for large-scale paper bag production, primarily for the manufacture of construction material bags, chemical material packaging, and food packaging bags.
- Customization: Can be customized to include 2-color, 4-color, or 6-color printing machines based on customer needs.
- High Speed: The printing speed can reach up to 150 m/min, ensuring high efficiency in large-volume production and reducing labor costs.
Inline printer used in the multi-wall paper bag production line
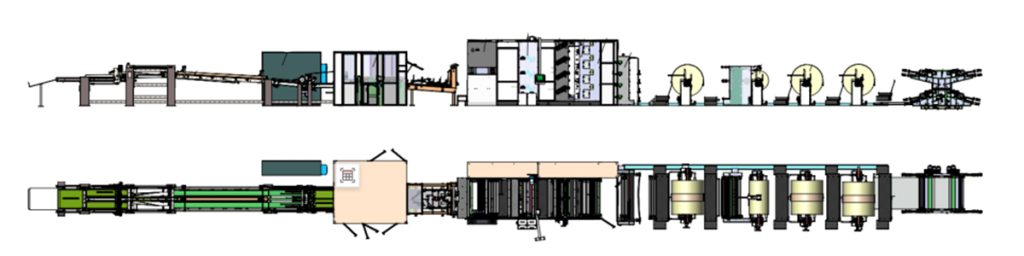
Specifications
Max. paper width | 1310mm |
Max. printing width | 1260mm |
Printing repeat | 279.4-1200.15mm |
Gearing | 1/8'CP,gear pitch 3.175mm |
Max. unwind diameter | Ø60" (1524 mm) |
Max. rewind diameter | Ø60" (1524 mm) |
Unwinder type | Shaftless unwinder,motorized lifting |
Rewinder type | Central tension control rewinder |
Max. mechanical speed | 150m/min |
Plate thickness | 1.7mm (TBD depending on customer's requirements) |
Tape thickness | 0.38mm (TBD depending on customer's requirements) |
Substrate | 60-200gsm paper printing |
Printing press color | White & orange colour |
Control language | English/Chinese |
Lubricating system | Automatic lubricationWith time and quantity adjustmentIndicator light automatically alarms when there is a lack of lubrication or system failure |
Control panel | Located in the front of the press |
Air pressure | 6-8kg (clean,dry,water-free and oil-free compressed air) |
Power requirement | 380 VAC+/-10% 3PH 50Hz |
Tension control range | 10-60kg |
Tension control tolerance | +/-2kg |
Ink supply | Automatic circulation |
Drying method | Electric heating and drying |
Dryer temperature | 120℃ |
Main drive | High precision gear with drive shaft transmissionBearings are mainly from NSK,NAICH,CCVI,etc. |
Features
Advanced Digital Control Technology
Utilizes advanced digital control technology to achieve automatic tension compensation.
High-Precision Ceramic Anilox Rollers
Features high-precision ceramic anilox rollers for even ink distribution, with a specially designed ink doctor blade that ensures uniform printing colors while reducing ink usage.
Integrated Printing Press Frame
The printing press frame is cast as a single unit, offering high precision and minimal vibration during high-speed operation, ensuring excellent register accuracy between each color.
Enhance your packaging process with high-quality printing solutions.
Contact us today to learn how the Inline Printer can improve your production efficiency and packaging quality.