Valve Pocket Bag Making Machines: A Comprehensive Guide to Features, Applications, and Benefits
Valve pocket bags, widely used for packaging powdered or granular materials such as cement, flour, chemicals, and fertilizers, require specialized machinery for efficient production. A valve pocket bag making machine is engineered to automate the manufacturing process, ensuring precision, speed, and consistency. This article explores the functionality, key features, and industrial applications of these advanced machines.
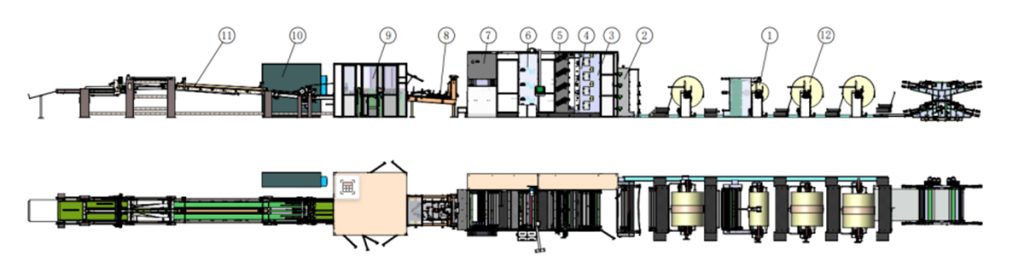
How Valve Pocket Bag Making Machines Work
Valve pocket bag making machines integrate cutting-edge technology to convert raw materials like polypropylene (PP), polyethylene (PE), or kraft paper into high-quality valve bags. The process typically involves:
- Material Feeding: Rolls of substrate are fed into the machine.
- Tube Formation: The material is folded and sealed vertically to form a tubular structure.
- Valve Attachment: A one-way valve is precision-installed to enable controlled filling while preventing material spillage.
- Printing (Optional): Custom logos, barcodes, or product information are printed inline.
- Cutting and Sealing: The tube is cut into individual bags, with bottom seals created via heat or ultrasonic methods.
- Stacking and Packaging: Finished bags are automatically counted and stacked for shipment.
Key Features of Modern Valve Pocket Bag Machines
- High Automation: Advanced PLC controls and servo-driven systems minimize manual intervention, boosting productivity.
- Precision Engineering: Laser-guided alignment ensures accurate valve placement and consistent bag dimensions.
- Multi-Layer Compatibility: Capable of producing 2- to 5-layer laminated bags for enhanced durability and moisture resistance.
- Quick Changeover: Modular designs allow rapid adjustments for different bag sizes, materials, or valve types.
- Energy Efficiency: Optimized power consumption reduces operational costs.
- Durability: Robust construction with corrosion-resistant components ensures long-term reliability in demanding environments.
Industrial Applications
Valve pocket bags are indispensable across sectors requiring secure, dust-free packaging:
- Construction: Cement, gypsum, and dry mortar.
- Agriculture: Fertilizers, animal feed, and seeds.
- Chemicals: Powders, resins, and industrial compounds.
- Food Processing: Flour, sugar, and additives.
- Pharmaceuticals: Granulated active ingredients or excipients.
Advantages of Using Valve Pocket Bag Machines
- Enhanced Productivity: Speeds up to 120 bags per minute meet high-volume demands.
- Cost Savings: Reduced material waste and labor costs improve ROI.
- Superior Quality: Uniform seals and valve integrity prevent leaks and contamination.
- Sustainability: Supports eco-friendly materials like recyclable PP or biodegradable films.
- Customization: Adaptable to customer-specific requirements for valve type, handle attachments, or anti-static features.
Conclusion
Valve pocket bag making machines are critical assets for industries prioritizing efficient, reliable, and customizable packaging solutions. By combining automation with precision, these machines streamline production while maintaining stringent quality standards. Investing in a well-designed valve bag machine not only optimizes operational workflows but also positions businesses to meet evolving market demands for sustainable and functional packaging.