Innovations and Processes in Modern Dust Extraction Paper Bag Manufacturing Lines
Release time:2025-05-14 Classification:Knowledge
The production of dust extraction paper bags is a specialized industrial process that combines precision engineering, material science, and sustainability principles. These bags are critical components in filtration systems used across industries such as woodworking, metal processing, and construction, where efficient dust collection is essential for workplace safety and regulatory compliance. This article explores the advanced methodologies, machinery, and quality control measures involved in a state-of-the-art dust extraction paper bag production line.
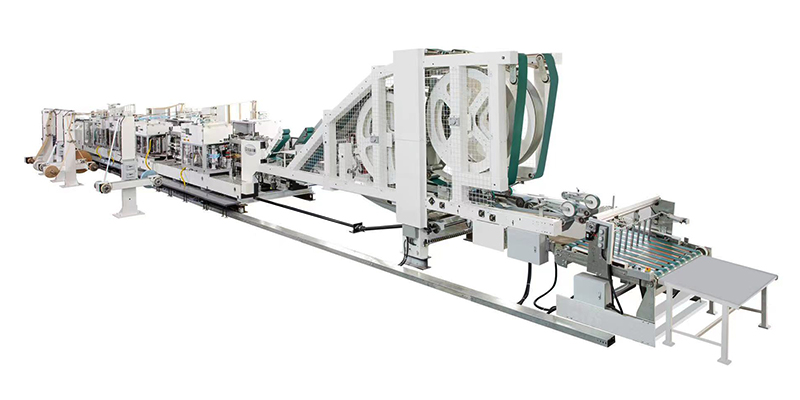
Key Components of a Dust Extraction Paper Bag Production Line
- Raw Material Preparation
The foundation of high-performance dust extraction bags lies in the selection of durable, breathable materials. Primary inputs include:
- Filter-grade paper: Engineered for optimal particle retention and airflow, often laminated or treated with water-resistant coatings.
- Reinforcement fibers: Synthetic or natural fibers integrated to enhance tear resistance and longevity.
- Adhesives: Heat-activated or solvent-free bonding agents for seam integrity.
- Conductive elements (optional): Embedded materials to dissipate static electricity in explosive environments.
- Automated Bag Forming Systems
Modern lines utilize servo-driven machinery to convert raw materials into precise bag geometries. Key stages include:
- Web unwinding: Controlled feeding of paper rolls into the production flow.
- Pleating/Corrugation: Creating uniform surface patterns to maximize filtration area.
- Tube formation: Overlapping edges with adhesive application for cylindrical shapes.
- Bottom sealing: Ultrasonic welding or heat pressing for leak-proof bases.
- Customizable Printing and Branding
Integrated digital printing units apply logos, safety labels, or capacity indicators without compromising material integrity. UV-cured inks ensure smudge-resistant markings suitable for harsh environments. - Anti-Static and Fire-Retardant Treatments
For hazardous applications, inline coating systems apply:
- Carbon-based conductive layers
- Intumescent compounds for fire resistance
- Antimicrobial agents in healthcare settings
- Quality Assurance Protocols
Multi-stage inspection systems guarantee compliance with ISO 16890 and ASHRAE standards:
- Air permeability testing: Measuring CFM/ft² at specified pressure differentials.
- Burst strength analysis: Hydraulic pressure tests to verify structural limits.
- Particle capture validation: Using standardized dust loads to assess efficiency.
Technological Advancements in Production
Recent innovations have transformed traditional manufacturing approaches:
- AI-Driven Predictive Maintenance: Vibration sensors and thermal imaging detect equipment anomalies before failures occur, minimizing downtime.
- Energy Recovery Systems: Capturing waste heat from drying stages to preheat incoming materials, reducing energy consumption by up to 30%.
- Adaptive Pleating Algorithms: Dynamic adjustment of pleat depth based on real-time material thickness measurements.
- Closed-Loop Recycling: Reprocessing trim waste into secondary products like filter cartridges or insulation materials.
Sustainability Considerations
Environmentally conscious manufacturing practices are now integral to production lines:
- Biodegradable Material Integration: Using FSC-certified papers and plant-based adhesives.
- Water-Based Coating Systems: Eliminating VOC emissions compared to solvent alternatives.
- Solar-Powered Facilities: Renewable energy integration in progressive manufacturing plants.
- Lightweighting Strategies: Reducing material use while maintaining performance through advanced structural simulations.
Applications and Customization
Modern lines accommodate diverse operational requirements:
- Size Variants: From 4" diameter bags for small workshops to 24" industrial units.
- Temperature Ratings: Producing bags resistant to temperatures ranging from -40°F to 500°F.
- Specialized Designs:
- Anti-microbial variants for food processing
- Oil-resistant models for metalworking fluids
- Static-dissipative configurations for explosive dusts
Future Trends in Production
Emerging technologies are reshaping the industry landscape:
- Nanofiber Integration: Electrospinning techniques to create ultra-fine filtration layers.
- Smart Bags with IoT Sensors: Embedded RFID tags tracking usage hours and pressure drop.
- 3D-Printed Seam Technology: Eliminating traditional glued joints for enhanced durability.
- Blockchain Traceability: Immutable material sourcing records for sustainability reporting.
The evolution of dust extraction paper bag manufacturing lines reflects broader industrial trends toward automation, sustainability, and smart technology integration. By combining robust engineering with ecological responsibility, modern production systems deliver filtration solutions that meet increasingly stringent performance and environmental standards. As industries worldwide prioritize cleaner production methods and worker safety, advancements in these manufacturing processes will continue to play a pivotal role in global dust management strategies.
This comprehensive approach ensures that end-users receive reliable, efficient filtration media while manufacturers maintain cost-effectiveness and regulatory compliance—a balance critical to the future of industrial air quality management.