Energy-Efficient Paper Bag Production Line: Sustainable Manufacturing Solutions
Release time:2025-05-10 Classification:Knowledge
The global shift toward eco-friendly packaging has driven demand for energy-efficient paper bag production lines. These advanced systems prioritize sustainability while maintaining high output, offering manufacturers a competitive edge in an increasingly environmentally conscious market. Here’s an in-depth look at how modern energy-efficient paper bag production lines operate and their benefits.
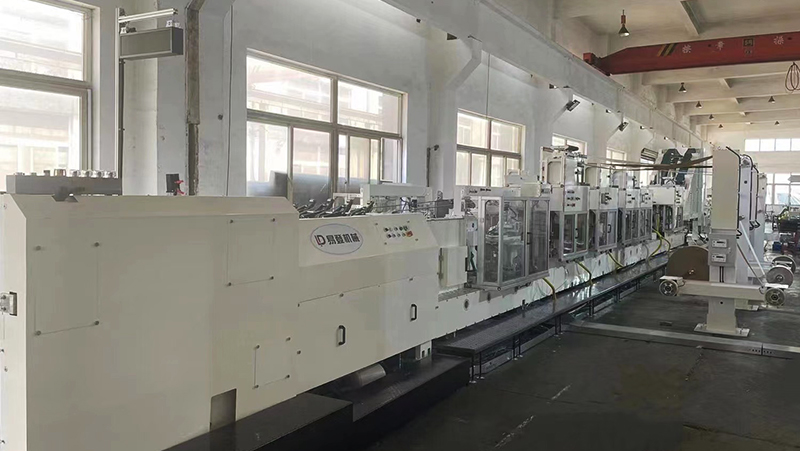
1. The Importance of Energy Efficiency in Paper Bag Manufacturing
Energy efficiency is critical in reducing operational costs and minimizing environmental impact. Traditional paper bag manufacturing often relies on energy-intensive processes, but modern production lines integrate innovative technologies to optimize energy use. By leveraging automation, precision engineering, and renewable energy sources, these systems reduce power consumption by up to 30% compared to conventional methods.
2. Key Components of an Energy-Efficient Production Line
- Advanced Drying Systems: Modern lines utilize infrared or air-impingement drying technologies, which require less energy while accelerating the drying process.
- Smart Automation: Sensor-driven machinery adjusts operations in real time, eliminating energy waste during idle periods or material transitions.
- Regenerative Braking Systems: Integrated in motor-driven components, these systems capture and reuse energy, further lowering overall consumption.
3. Sustainable Material Integration
Energy-efficient production lines often pair with recycled or FSC-certified paper, reducing reliance on virgin materials. This synergy ensures lower carbon footprints while maintaining product durability. Additionally, water-based adhesives and soy inks are prioritized to align with eco-friendly manufacturing standards.
4. Waste Reduction and Circular Design
Modern systems incorporate closed-loop processes to recycle scrap paper and trimmings back into production. This minimizes waste and raw material costs. Energy recovery units also convert excess heat from machinery into reusable energy, supporting a circular economy model.
5. Long-Term Benefits for Manufacturers
Investing in an energy-efficient paper bag production line yields significant advantages:
- Cost Savings: Reduced energy and material expenses improve profit margins.
- Regulatory Compliance: Meets stringent environmental regulations and carbon emission targets.
- Market Appeal: Aligns with consumer preferences for sustainable packaging, enhancing brand reputation.
6. Future Trends in Energy-Efficient Manufacturing
Emerging technologies, such as AI-driven predictive maintenance and solar-powered production units, are set to further revolutionize the industry. These innovations will enable manufacturers to achieve near-zero emissions while scaling output.
Adopting an energy-efficient paper bag production line is no longer optional but a strategic necessity. By combining cutting-edge technology with sustainable practices, manufacturers can reduce costs, comply with global standards, and contribute to a greener future. As demand for eco-friendly packaging grows, these systems will play a pivotal role in shaping the industry’s trajectory.