Comprehensive Guide to Food Grade Paper Bag Production Line: Processes, Materials, and Quality Standards
Release time:2025-05-10 Classification:Knowledge
The demand for sustainable and food-safe packaging solutions has driven significant advancements in the manufacturing of food grade paper bags. A dedicated production line for food grade paper bags ensures compliance with strict hygiene and safety standards while delivering eco-friendly packaging options. This article explores the key components, processes, and quality controls involved in a modern food grade paper bag production line.
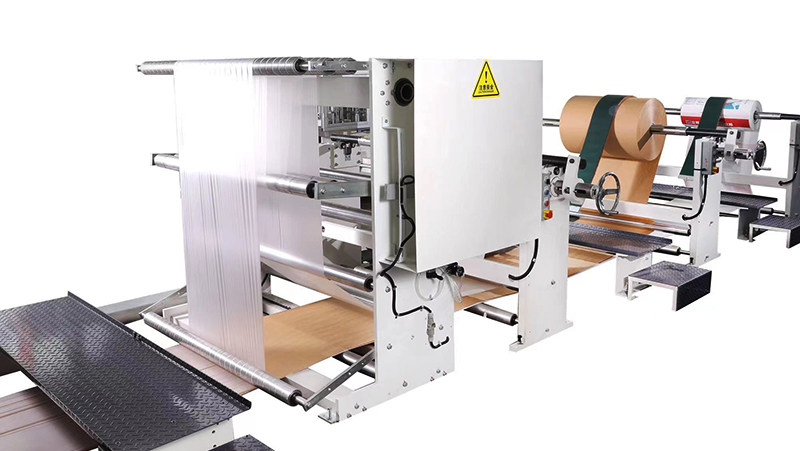
Key Components of a Food Grade Paper Bag Production Line
- Raw Material Selection
Food grade paper bags require specialized materials to meet safety regulations. The primary material is kraft paper, sourced from responsibly managed forests and certified for food contact. The paper must be free from harmful chemicals, bleach, or additives, ensuring it complies with FDA, EU, or other regional food safety standards. - Printing and Customization
High-speed flexographic printing units are integrated into the production line to apply designs, logos, or branding. Food-safe, water-based inks are used to prevent contamination. Advanced systems ensure precise color matching and alignment, even for multi-layer designs. - Die-Cutting and Bag Forming
Rotary die-cutting machines shape the paper into precise bag dimensions. The production line then folds and glues the paper using food-grade adhesives, forming flat or satchel-style bags. Heat-sealing technology may be applied for reinforced edges or gusseted designs. - Quality Control Systems
Automated inspection systems monitor thickness, print accuracy, and structural integrity. Bags undergo rigorous testing for tensile strength, grease resistance, and barrier properties (if lined). Microbial testing ensures compliance with food hygiene protocols. - Packaging and Sterilization
Finished bags are bundled in cleanroom conditions. Some lines incorporate UV sterilization or ozone treatment to eliminate pathogens before final packaging.
Critical Standards for Food Grade Compliance
- Material Certification: Paper must meet ISO 22000, BRCGS, or equivalent food safety certifications.
- Ink and Adhesive Safety: Components must be non-toxic and approved for indirect food contact.
- Production Environment: Dust-controlled facilities with HACCP protocols to prevent cross-contamination.
Sustainability Advantages
Modern food grade paper bag production lines prioritize eco-efficiency. Renewable materials, energy-saving machinery, and recyclable outputs align with global circular economy goals. Many systems also integrate waste-reduction technologies, repurposing paper scraps into new batches.
Applications in the Food Industry
Food grade paper bags are widely used for:
- Bakery items (bread, pastries)
- Dry goods (grains, snacks)
- Fresh produce (fruits, vegetables)
- Takeaway and delivery services
A well-optimized food grade paper bag production line combines advanced automation, stringent safety checks, and sustainable practices. By adhering to international food contact standards and leveraging innovative manufacturing technologies, producers can deliver packaging that protects both consumer health and the environment. As regulations evolve, continuous investment in R&D remains crucial to maintaining compliance and market competitiveness.