IoT Integration in Paper Bag Manufacturing: Real-Time Monitoring Case Studies
Release time:2025-04-27 Classification:Knowledge
The paper bag manufacturing industry, traditionally reliant on manual processes and fragmented data management, is undergoing a transformative shift with the integration of Industrial Internet of Things (IIoT) technologies. By leveraging real-time monitoring, predictive analytics, and interconnected systems, manufacturers are achieving unprecedented efficiency, cost reduction, and operational agility. This article explores key case studies and technological advancements driving IoT adoption in this sector.
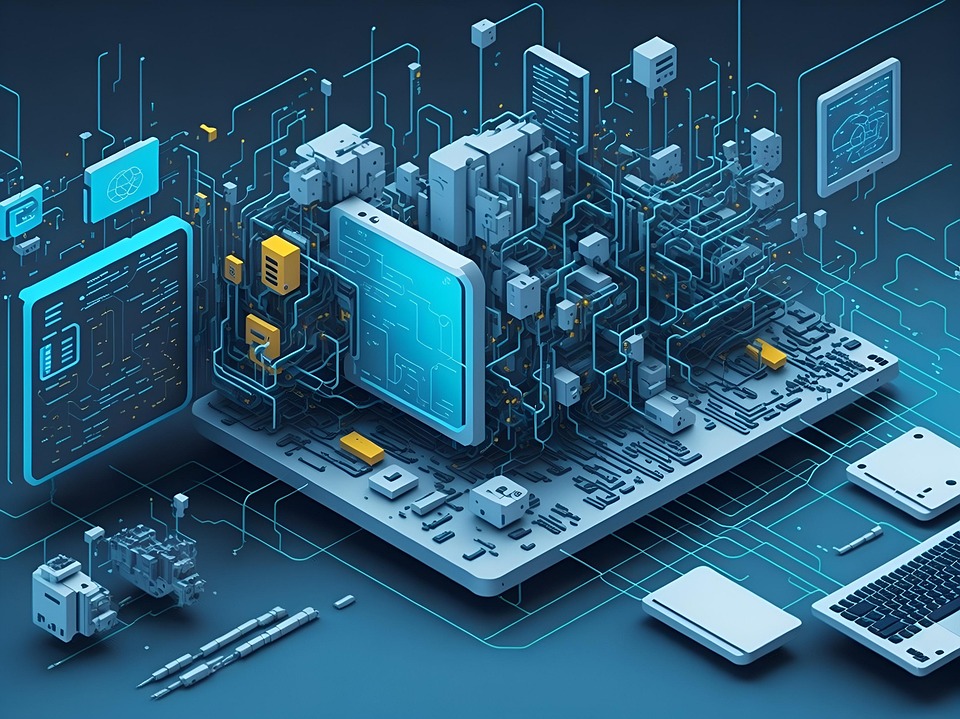
1. Real-Time Production Monitoring and Automated Data Collection
Real-time monitoring of machinery and production lines is a cornerstone of IoT integration in paper bag manufacturing. For instance, Stepke’s Machine IoT (M-IoT) Solution exemplifies this approach. In a case involving a Chinese woven bag manufacturer with over 3,000 circular looms, Stepke deployed IoT-enabled touchscreens (GT series) connected to edge servers. These devices automated data collection, replacing manual logging of parameters like machine speed, output, and downtime. The system enabled instant visibility into production progress, reduced human error, and allowed remote parameter adjustments for different bag specifications. Real-time dashboards provided managers with actionable insights, improving coordination and reducing idle time by 15–20%.
Similarly, Turck’s Smart I/O Monitoring System addressed challenges in paper press monitoring. Traditional optical sensors often misidentified human movement or forklifts as paper bales, leading to false alarms. Turck’s solution integrated laser distance sensors with ARGEE-programmable I/O modules, enabling precise detection of bale accumulation. By setting timers (e.g., 45-second intervals), the system eliminated false triggers and automatically alerted workers via LED indicators when intervention was needed. This reduced manual checks by 70% and enhanced safety in high-risk areas.
2. Predictive Maintenance and Equipment Health Management
IoT-enabled predictive maintenance minimizes unplanned downtime, a critical factor in high-volume paper bag production. Siemens’ IoT Implementation (cited in broader industrial automation contexts) demonstrates how vibration and temperature sensors on machinery feed data into AI models to predict equipment failures. For example, anomalies in motor performance or bearing wear are flagged days in advance, allowing preemptive repairs. In paper bag manufacturing, such systems could reduce downtime by 40–50% and maintenance costs by 20%.
A specific application involves digital twin technology, where virtual models of production lines simulate real-world conditions. By combining IoT sensor data with AI analytics, manufacturers can test maintenance strategies in a risk-free environment. For instance, a digital twin of a paper-cutting machine might identify optimal blade replacement schedules, extending equipment lifespan by 15% while maintaining output quality.
3. Resource Optimization and Energy Efficiency
IoT systems optimize raw material usage and energy consumption. In one case, a chemical manufacturer (analogous to paper bag producers) used IoT sensors to track resin consumption, identifying inefficiencies in material distribution. Adjustments to nozzle pressure and conveyor speeds reduced waste by 12%.
Energy management is another critical area. GE’s IIoT Solutions highlight how real-time monitoring of power consumption across machines enables dynamic adjustments. For example, during off-peak hours, IoT algorithms might slow non-critical machines, cutting energy costs by 10–15% without affecting output.
4. Quality Control and Defect Detection
Computer vision integrated with IoT platforms enhances quality assurance. Tesla’s AI-Driven Production (adapted to paper bag manufacturing) uses cameras and machine learning to inspect bags for defects like uneven seams or ink misalignment. Real-time feedback loops adjust production parameters, reducing defect rates by 30–50%.
In a specialized case, Bayesian Continuous Wavelet Transform (developed by Lanzhou University) analyzes vibration data from paper-converting machinery to detect subtle anomalies. This method, validated in structural health monitoring, could predict blade misalignment in real time, preventing defective batches.
5. Challenges and Future Directions
Despite these advancements, challenges persist:
- Data Silos: Legacy machinery with proprietary protocols complicates IoT integration. Solutions like Info-Tech’s Connected Factory Blueprint recommend hybrid cloud-edge architectures to unify IT/OT systems.
- Security Risks: Increased connectivity exposes factories to cyber threats. Implementing network segmentation (e.g., dual Ethernet ports in Stepke’s M-IoT) and encrypted APIs is critical28.
- Skill Gaps: Workforce training in IoT analytics remains a barrier. Partnerships with tech providers (e.g., ABB’s training programs) are bridging this gap.
Future trends include 5G-enabled IoT for ultra-low latency communication and AI-enhanced digital twins for autonomous decision-making. For instance, 5G could enable real-time adjustments across distributed paper bag plants, while AI might autonomously reroute production during supply chain disruptions.
Conclusion
IoT integration in paper bag manufacturing is no longer a futuristic concept but a present-day imperative. Through real-time monitoring, predictive analytics, and intelligent automation, manufacturers are achieving leaner operations, higher quality, and sustainable growth. As technologies like 5G and digital twins mature, the industry will continue to evolve, setting new benchmarks for efficiency and innovation.