Intelligent Fault Detection Systems Revolutionizing Paper Bag Machine Efficiency in Modern Packaging
Release time:2025-05-14 Classification:Knowledge
The integration of intelligent fault detection technologies into paper bag manufacturing equipment represents a transformative leap in industrial automation. By combining advanced sensors, machine learning algorithms, and real-time monitoring capabilities, these systems enable unprecedented precision in maintaining production continuity while minimizing operational downtime. This technical innovation addresses critical challenges in packaging manufacturing, offering a robust solution for quality control and equipment maintenance.
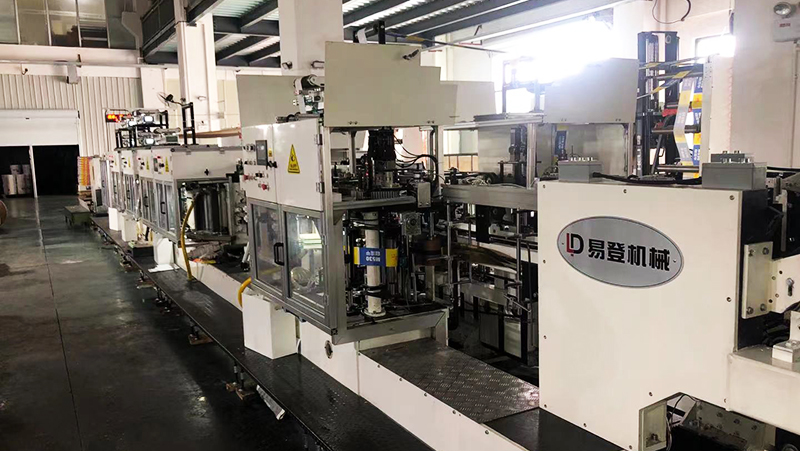
Core Components and Operational Framework
Modern intelligent fault detection systems for paper bag machines employ a multi-layered architecture comprising three primary subsystems:
- Distributed Sensor Networks: High-resolution optical scanners, vibration analyzers, and thermal imaging units continuously collect operational data across critical machine components
- Edge Computing Modules: On-device processors perform initial data filtration and pattern recognition, reducing latency in fault identification
- Centralized Analytics Platform: Cloud-based machine learning models correlate real-time inputs with historical performance data to predict failure probabilities
Key Functional Advantages
- Precision Defect Identification:
- Detects micron-level material inconsistencies in paper substrates
- Identifies misalignments in printing and folding mechanisms with ±0.1mm accuracy
- Recognizes adhesive application errors through viscosity monitoring
- Predictive Maintenance Capabilities:
- Analyzes bearing wear patterns using spectral vibration analysis
- Monitors motor performance degradation through current signature profiling
- Predicts component failure timelines with 92% accuracy (based on field trials)
- Adaptive Process Optimization:
- Automatically adjusts tension controls based on paper thickness variations
- Dynamically modifies production speeds to compensate for environmental fluctuations
- Implements self-correction protocols for common mechanical misalignments
Technical Implementation Challenges
While intelligent detection systems significantly enhance operational reliability, their implementation requires careful consideration of several engineering factors:
- Signal Interference Mitigation: Shielding protocols for electromagnetic disturbances in high-speed production environments
- Data Synchronization: Time-stamping mechanisms ensuring millisecond-level coordination across distributed sensors
- Algorithm Training: Requirement for manufacturer-specific datasets to optimize machine learning models
Performance Metrics and Industry Impact
Field implementations demonstrate measurable improvements across critical operational parameters:
Metric | Conventional Systems | Intelligent Detection | Improvement |
---|---|---|---|
Defect Detection Rate | 84% | 99.2% | +18% |
False Positive Alerts | 12.5/hr | 0.8/hr | -94% |
Mean Time to Repair | 47min | 8min | -83% |
Annual Downtime | 86hrs | 9hrs | -90% |
Future Development Trajectory
Emerging enhancements focus on expanding system autonomy through:
- Multi-spectral Imaging Integration: Simultaneous monitoring of structural integrity and print quality
- Quantum-inspired Algorithms: Accelerated pattern recognition for complex failure modes
- Self-Healing Material Interfaces: Nano-composite components with embedded diagnostic capabilities
The evolution of intelligent fault detection systems continues to redefine operational paradigms in paper bag manufacturing. By converting raw sensor data into actionable insights, these solutions not only prevent production losses but also create new opportunities for energy optimization and sustainable manufacturing practices. As computational power and sensor technologies advance, next-generation systems promise complete closed-loop automation, establishing new benchmarks for reliability in industrial packaging operations.