How to Optimize Paper Bag Machine Efficiency in 2025
Release time:2025-04-27 Classification:Knowledge
The paper bag manufacturing industry is undergoing rapid transformation, driven by advancements in automation, smart technologies, and sustainability demands. Optimizing machine efficiency in 2025 requires a holistic approach that integrates cutting-edge innovations with strategic operational practices. Below, we explore actionable strategies to enhance productivity, reduce downtime, and improve the flexibility of paper bag machines.
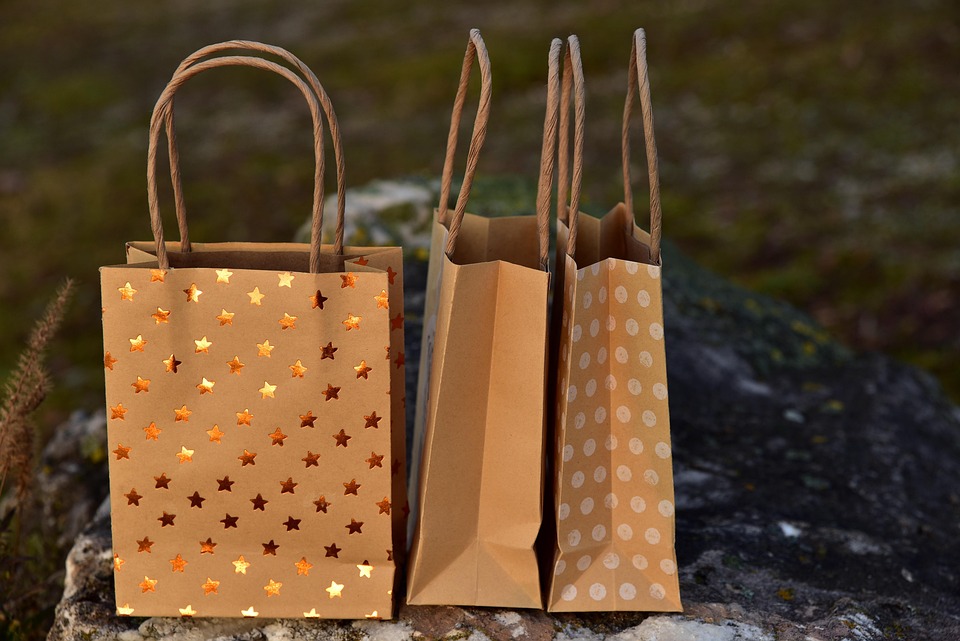
1. Embrace Smart Automation and Integrated Control Systems
Modern paper bag machines benefit from intelligent automation that combines hardware, software, and real-time data analytics. For instance:
- Embedded Motion Control: Integrating servo drives with embedded controllers reduces panel space and simplifies synchronization between axes, enabling precise control over cutting, folding, and gluing processes. This minimizes material waste and ensures consistent output quality.
- Open Architecture Systems: Open protocols like IO-Link® allow seamless communication between sensors, actuators, and controllers. Real-time data from devices such as photoelectric sensors or temperature monitors can optimize machine performance and streamline changeovers8.
- Safety Integration: Advanced safety functions, such as Safe Torque Off (STO) and Safe Stop 1 (SS1), are now embedded directly into drives, eliminating the need for external safety modules. This reduces wiring complexity and improves response times during emergencies.
2. Implement Predictive Maintenance and Condition Monitoring
Unplanned downtime remains a critical challenge. In 2025, predictive maintenance technologies are indispensable:
- Wear Monitoring Systems: Inspired by solutions like Voith’s Seal Wear Monitoring, sensors embedded in critical components (e.g., rollers or seals) track wear patterns and predict failure points. This allows maintenance teams to schedule replacements during planned downtime, avoiding costly breakdowns.
- Remote Diagnostics: Cloud-connected systems enable real-time monitoring of motor health, lubrication levels, and vibration data. Alerts for anomalies, such as overheating or misalignment, can be sent directly to maintenance personnel via email or dashboards.
3. Optimize Motion Control and Synchronization
Precision in motion control directly impacts throughput and material handling efficiency:
- High-Performance Servo Drives: Dual-axis servo systems, like the Kollmorgen AKD2G, double power density while reducing footprint by 20%. These drives support synchronized multi-axis operations, essential for high-speed bag forming and printing.
- Adaptive Speed Control: Variable Frequency Drives (VFDs) and soft starters reduce mechanical stress during motor startups, extending equipment lifespan and cutting energy consumption by up to 30%7.
4. Enhance Flexibility for Customized Production
Consumer demand for personalized packaging requires flexible manufacturing systems:
- Modular Design: Machines with interchangeable tooling and programmable logic controllers (PLCs) enable rapid reconfiguration for different bag sizes, materials, or designs. This aligns with the trend toward small-batch, high-mix production.
- Human-Machine Interfaces (HMIs): Intuitive graphical programming environments allow operators to adjust parameters on-the-fly without specialized coding skills. For example, HMI-driven workflows can automate adjustments for paper thickness or adhesive application rates.
5. Prioritize Environmental Stability and Energy Efficiency
Environmental factors significantly impact machine accuracy and longevity:
- Temperature and Humidity Control: Maintain workshop conditions at 15–25°C and 40–60% RH to prevent paper warping or adhesive curing issues. Precision climate systems also reduce thermal expansion errors in mechanical components.
- Energy-Efficient Motors: Upgrading to IE4-class motors or regenerative drives recovers energy during deceleration phases, cutting operational costs by 15–20%.
6. Leverage Data-Driven Decision-Making
The rise of Industry 4.0 tools enables smarter resource allocation:
- Real-Time Dashboards: Platforms like Banner Engineering’s Snap Signal® convert legacy machine data into actionable insights. Metrics such as Overall Equipment Effectiveness (OEE) highlight bottlenecks in production lines8.
- AI-Powered Analytics: Machine learning algorithms analyze historical data to optimize production schedules, predict material requirements, and reduce scrap rates. For example, AI can adjust cutting patterns to minimize paper waste based on real-time roll dimensions.
Conclusion
In 2025, optimizing paper bag machine efficiency hinges on integrating smart technologies, predictive maintenance, and adaptive production systems. By leveraging advancements in motion control, IoT connectivity, and energy management, manufacturers can achieve higher throughput, reduced downtime, and greater flexibility to meet evolving market demands. As the industry moves toward fully autonomous "smart factories," investing in these strategies today will ensure competitiveness in tomorrow’s sustainable packaging landscape.